PRÊMIO FINEP 2005
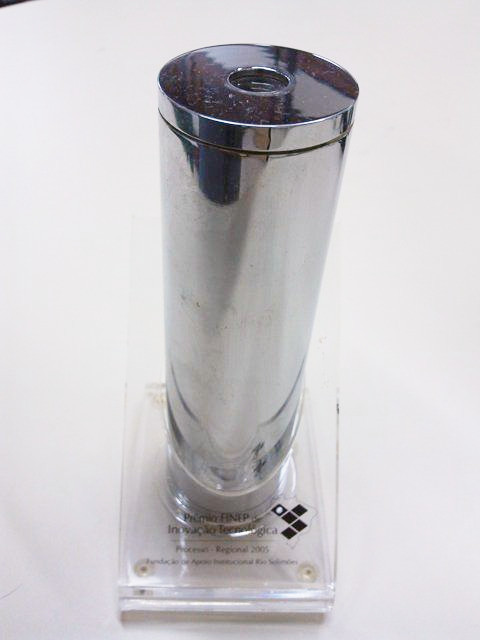
Categoria
Processos
Colocação
Segunda
Título do Projeto
Desenvolvimento de uma Unidade para Transporte Eficiente de Materiais – PUSH CAR
Resumo do projeto
Para o transporte de módulos de Displays de Cristal Líquido entre a Philips MDS e seus clientes, a empresa seguia um processos convencional de embalagem dos Displays de Cristal Líquido em cartelas plásticas, incluindo 30 ou 32 unidades por cartela. Em seguida, essas cartelas eram agrupadas em conjuntos de 10 ou 12 unidades sendo embaladas em caixas e paletizadas. No cliente, os displays eram desembalados e utilizados para a montagem do celular. As cartelas, devido ao processo de paletização e transporte, chegavam no cliente amassadas. Assim, após o uso, tanto as cartelas quanto as caixas utilizadas na paletização eram jogadas no lixo. Esse projeto teve por objetivo propor uma unidade de transporte que evita a danificação e que permite reaproveitar as cartelas. Com isso conseguiu-se uma economia substancial de materiais e a simplificação da etapa final do processo produtivo. Traduzindo melhor, a empresa fez uma economia significativa em termos de unidades de cartelas utilizadas para embalagem dos displays de cristal líquido, embalagens de papelão e demais acessórios utilizados no processo de paletização. Além disso, a etapa final de paletização foi eliminada do processo produtivo. A solução encontrada foi o projeto de uma unidade de transporte de cartelas com os seguintes requisitos funcionais: transporte seguro sem danificação das cartelas e transporte sem riscos de descargas eletrostáticas. Utilizando softwares para modelagem e simulação mecânicos, projetou-se uma unidade de transporte com capacidade de transportar até 180 cartelas acomodadas em nichos delimitados por guias mecânicas. Em cada nicho são acomodadas dez cartelas. Na unidade de transporte existe um total de 18 nichos, formando um retângulo de 3x6. A parte da frente de cada um desses nichos é limitada pela própria porta da unidade, o que impede o deslocamento das cartelas durante o transporte. Um cabo de aterramento pendurado na parte inferior da unidade e rodízios apropriados impedem a existência de descargas eletrostáticas. Para que haja um transporte seguro no veículo que leva essas unidades da empresa produtora, a Philips MDS para as empresas clientes, a Nokia e a Siemens, as rodas dessa unidade de transporte têm a possibilidade de travamento. A fim de conferir rigidez e durabilidade ao conjunto, utilizou-se como elemento construtivo o aço inox. Para diminuir o peso da estrutura utilizou-se tubos e barras chatas de 2mm. O peso total da unidade vazia é de 60 Kg. O peso da unidade carregada é de aproximadamente 200Kg. Outra preocupação pertinente foi com as dimensões da unidade. A fim de garantir uma boa estabilidade da mesma, foi essencial dimensionar uma razão adequada entre a altura e as outras dimensões paralelas ao plano do chão. Através de simulações computacionais de estabilidade chegou-se aos seguintes valores ótimos que foram utilizados no projeto: 1,50m altura x 1,18m comprimento x 0,52 de largura. Para absorver os riscos do transporte quanto a possíveis impactos que a unidade pudesse vir a sofrer, utilizou-se rodízios com amortecedores. Essa solução, ao permitir a absorção das vibrações ocorridas durante o transporte, impactou tanto na estabilidade da unidade quanto na segurança dos displays transportados. Ressaltamos, por fim, as preocupações com a ergonomia do projeto, no sentido da facilidade de condução e acesso ao meio interno. Em uma das extremidades da unidade existe uma barra, numa altura que levou em consideração a altura média dos operadores do processo, que permite a condução da mesma de forma confortável. As portas da unidade ao abrirem permitem um amplo acesso a todo o interior da unidade. Existe a possibilidade de abertura de apenas uma das portas. As portas têm sistema de trava que impedem a abertura durante o transporte. Nas figuras abaixo mostramos fotos do projeto desenvolvido:
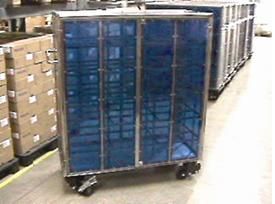
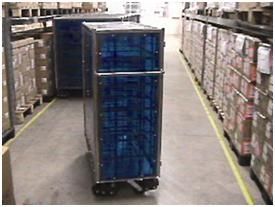
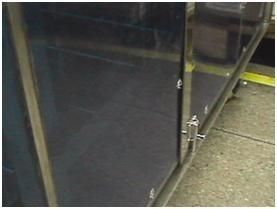
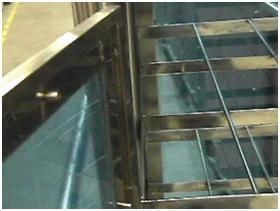
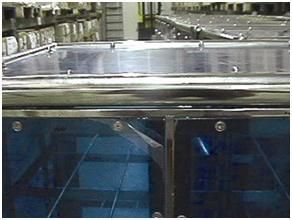
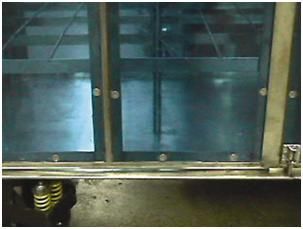
Redes Sociais